- Docente: Andrea De Pascale
- Credits: 6
- SSD: ING-IND/08
- Language: English
- Moduli: Andrea De Pascale (Modulo 1) Lisa Branchini (Modulo 2)
- Teaching Mode: Traditional lectures (Modulo 1) Traditional lectures (Modulo 2)
- Campus: Bologna
-
Corso:
Second cycle degree programme (LM) in
Automation Engineering (cod. 8891)
Also valid for Second cycle degree programme (LM) in Mechanical Engineering (cod. 5724)
-
from Feb 22, 2023 to May 24, 2023
-
from May 31, 2023 to Jun 09, 2023
Learning outcomes
The course aims to provide a basic knowledge of Hydraulics and Pneumatics industrially known as Fluid Power Systems, operating with mineral oils (or water based fluids) or with air as energy vectors, in order to transfer mechanical energy. The course provides design and operating principles of main components (pumps, actuators, valves, etc.) and systems, with special reference to high power fluid machines.
Course contents
1 Introduction on fluid power
Introduction on hydraulics and pneumatics. Transmissions and energy conversions. Examples of applications.
Hydrostatics and Hydrodynamics basic equations. Properties of fluids of interest for hydraulics and pneumatics: viscosity, compressibility and classifications of oils.
Symbols according to ISO standard 1219. Elementary hydraulic circuit. Examples of circuits.
2 Pumps for fluid power applications
Introduction: limitations of centrifugal pumps; characteristics of volumetric pumps; performance and losses; classification.
Gear pumps: external gear pump architecture; displacement generation; instantaneous flow calculation with an energetic approach; mean volumetric flow and pump displacement. Pulsating flow and pressure. Radial balancing and load on the shaft; axial balancing: fixed axial clearance pumps and floating pumps. The problem of determining the pressure in the space between teeth of a gear pump.
Practical exercise of disassembling gear pumps.
Other positive displacement pumps: Internal gear pumps, Gerotor pumps, screw pumps and lobe pumps: architectures.
Vane pumps: generation and expression of the displacement; shape of suction / discharge openings; variable displacement vane pump and characteristic curve.
Piston pumps: single-cylinder pump architecture. Multi-cylinder axial pumps with axial and radial pistons: architecture and generation of displacement. Expression of instantaneous flow rate and flow ripple of the multi-cylinder piston pumps.
Radial piston pumps: architectures with fixed cylinder block and with rotating block; variable displacement architectures.
3 Pumps regulators
Variable displacement pumps regulation: pressure limiter, circuit and diagram; constant power regulation. Load Sensing regulation.
Energy considerations on the use of fixed and variable displacement pumps: circuit with selector to manage two work phases; two pump circuit, circuit with multiple pumps. Power dissipation with variable displacement pump with pressure regulator and with load sensing regulator.
4 Actuators
Linear hydraulic and pneumatic actuators. Classification. Single and double acting cylinders; features ;hydraulic circuits. Braking system. Pressure multiplier. Design of the piston rod.
Rotary hydraulic motors. Torque and power characteristics. Examples of architectures: orbital motors, axial and radial piston motors, multi-piston piston engines.
Hydrostatic transmission: examples of open circuit and closed loop; mechanical characteristics.
5 Flow distribution valves
Introduction to distributors: functions, symbols, architectures, operating limits. Examples and diagrams of spool valves: 2/2, 3/2, 4/3. Lap conditions. Design of the spool and possible central positions.
Direct drive and control of the distributors. Mechanical and solenoid valve. Indirectly operated valves.
Spool valve with 4 piloting edges and negative lap: static characteristic curves.
Spool valve with 4 piloting edges and zero lap: characteristic equation and problems. Characteristic curves od the positive lap spool valve.
Spool valve and hydraulic motor system and transfer function.
Hydraulic power steering: scheme, transfer function and feedback.
6 Other control valves and basic hydraulic / pneumatic circuits
Pressure control valves. Pressure relief valves: architecture of poppet and spool valves, characteristic curve, pilot valve, system diagrams. Pressure reducing valves: valve architecture and function in the circuit.
Circuits with pressure control valves: sequence valves; back pressure valves; counterbalance valves, braking valves.
Flow control valves: types, functions and architectures of throttling valves. Circuits for speed control with flow control valves: "Meter-in", "Meter-out" and "Bleed-off".
Compensated flow control valves.
Regenerative connection for differential cylinders.
Actuator connections in series and in parallel. Examples of circuits for cylinder synchronization.
Flow dividers: architectures, functions, pressure intensifier.
Readings/Bibliography
The topics of the lectrures are based on the following texts:
Mannesmann, Rexroth, Manuale di oleodinamica (il) volume 1: fondamenti e componenti oleodinamici ristampa 1990, Mannesmann-Rexroth GmbH 0-8023-0619-8, 1990
Assofluid. Hydraulics in industrial and mobile applications. Milano 2007
Belladonna U. Elementi di Oleodinamica. Principi – componenti-impianti, Hoepli, Torino, 2001
Belladonna U., Mombelli A. Pneumatica, Hoepli, Torino, 2001
G. Bacchielli, F. Danielli, S. Sandrolini. Dinamica e controllo delle macchine a fluido. Pitagora, Bologna
Mannesmann, Rexroth, Manuale di pneumatica (il) volume 1: Fondamenti di pneumatica, ed. RI 00 296/10.90, Mannesmann-Rexroth GmbH, 1991
Teaching methods
Class Lectures (held in Italian) on the Course contents.
Lectures attendance is recommended, but it is not mandatory to pass the exam.
Assessment methods
Oral exam.
Individual oral exam, on the topics of the carried out lectures, with reference to:
1) functional aspects;
2) schemes of systems;
3) quantitative aspects and demonstrations.
The questions are aimed at the following learning outcomes:
knowledge of the main fluid power systems, components and design characteristics.
Higher grades will be awarded to students who demonstrate an organic understanding of the subject, a high ability for critical application, and a clear and concise presentation of the contents.
To obtain a passing grade, students are required to at least demonstrate a knowledge of the key concepts of the subject, some ability for critical application, and a comprehensible use of technical language.
A failing grade will be awarded if the student shows knowledge gaps in key-concepts of the subject, inappropriate use of language, and/or logic failures in the analysis of the subject.
The exam will be grade over the 0-30 range, with 18 the minimum to pass, 30 the maximum. Honor can be assigned.
Teaching tools
The use of overhead projector and pc is considered in order to draw schemes, to represent formulas and to show complex layouts, plant components and systems related with the course contents. All the projected content is available for students after the lectures.
Office hours
See the website of Andrea De Pascale
See the website of Lisa Branchini
SDGs
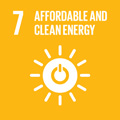
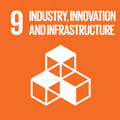
This teaching activity contributes to the achievement of the Sustainable Development Goals of the UN 2030 Agenda.