- Docente: Cristina Mora
- Credits: 3
- SSD: ING-IND/17
- Language: Italian
- Teaching Mode: Traditional lectures
- Campus: Bologna
- Corso: Second cycle degree programme (LM) in Engineering Management (cod. 0936)
-
from Sep 19, 2022 to Dec 19, 2022
Learning outcomes
At the end of the module the student will have to know the innovative and sustainable tools and methods for the "lean" management of industrial and tertiary production systems, both in terms of internal and external logistics flows, and of creating the continuous production flow pulled by the customer.
Course contents
This course aims to deepen the techniques and methodologies of Lean Manufacturing for the lean design of production systems, with particular attention to the operational management of production and the management of materials with a view to Total Flow Management.
Introduction to Total Flow Management (TFM) and lean supply chain principles. Total Flow Management: Quality First; Gemba Orientation; Waste elimination; People development; Visual standard; Pull Flow thinking. The pillars of TFM: Basic reliability; Supply chain design; Production Flow; Internal Logistic Flow. TFM tools and methods in the production process - the Production Flow pillar: line and layout design; line balancing; line edge design (flow container, design guidelines, examples); standard work; SMED; low cost automation.
Creating Continuous Flow: continuous flow processes. Designing a Continuous Flow Cell: Guidelines. Operator balance Chart (OBC); Guidelines for cell layout; guidelines for implants; guidelines for material management; sizing of operators and distribution of work (splitting work; circuit distribution; reverse flow; combination of work; one operator per station; harpoonism). TFM tools and methods in the production process - the Internal Logistics Flow pillar:
TFM tools and methods in the production process - the Internal Logistics Flow pillar: The tools: supermarket (flow rack, ground storage on wheel, the logistic cell, border of line supermarket, the kitting supermarket); sizing of supermarkets. How to decide the type of flow: class/flow assignment matrix. The flow types Just in Sequence (JIS), Just in Time (JIT), Indirect (IND).
Making Material Flow: implement a Lean management of materials. Analysis and design of the continuous flow in internal logistics: The plan for each component (PFEP); Designing the supermarket of components: storage means; the allocation system; procedures for placing and picking up components; procedures for reacting to inventories beyond the maximum level; define the minimum stock level and reorder points. Design the delivery route to the production area: define the corridors, choose the means of transport (Mizusumashi), stops and delivery points; design shelves at the point of delivery.
Design the information system for delivery: pull tags; frequency of delivery; coupled or decoupled path; number of pull tags. Exercise on the sizing of supermarkets and components; Tutorial on mizusumashi sizing; Exercise on the assignment of flows (Kanban and Junjo) and economic evaluation. Lean-green Supply Chain - Principles of Green production integrated with the principles of Lean production. The Tool of Sustainable Value Stream Mapping (SVSM): evolution and characteristics. Exercise on the construction of the SVSM applied to the ACME case.
Readings/Bibliography
EUCLIDES A. COIMBRA, “Total flow management. Kaizen per l'eccellenza nella supply chain e oltre”, Kaizen Institute Italia 2016.
M.ROTHER,, R.HARRIS, “Creating Continuous Flow”, The lean enterprise institute, Massachusetts (USA), 1999
R.HARRIS, C.HARRIS, E.WILSON, “Making Materials Flow”, The lean enterprise institute, Massachusetts (USA), 1999
A.SMALLEY, “Creating Level Pull”, The lean enterprise institute, Massachusetts (USA), 1999
D.JONES, J.WOMACK, ”Seeing the Whole Value Stream”, The lean enterprise institute, Massachusetts (USA), 2011.
J.BICHENO, A. PORTIOLI STAUDACHER, “Metodologie e tecniche per la lean”, Pitagora editrice, Bologna, 2009.
S.CORTIGLIONI, L.SALCERINI, D.VERGA, “Il successo Continuo- L’eccellenza Toyota dalla via Emilia all’Europa”, Hoepli, 2017.
J.MILLER, M.WROBLEWSKI, J.VILLAFUERTE, “Creating a kaizen culture – Align the organisation, achive breakthrough results and sustain the gains”, McGrawHill Education, 2014.
J. DUMSER, “Value Stream mapping – Reduce waste and maximise efficiency”, Business 50minutes.com
ROBERT MARTICHENKO AND KEVIN VON GRABE “Building a Lean Fulfillment Stream”, Lean Enterprise Institute, Inc., 2010.
M.IMAI, “Gemba Kaizen”- un approccio operativo alle strategie del miglioramento continuo”, Frano Angeli, 2015.
C.DONINI, “Lean Manufacturing – manuale per progettare e realizzare un’azienda snella”, Franco Angeli, 2019.
D.COGLIATI, “Lean Production per le aziende a commessa- Gestione e Ottimizzazione” Gruppo Galgano, 2019
Teaching methods
Classroom lessons; Lecture notes of the teacher, exercises of the teacher. Company visits and group project in the company.
Assessment methods
Written exam with 1 exercise and 1 theoretical question (duration 1.5 h) + presentation of a group project carried out in the company on the redesign of processes and / or logistics with a view to lean production (with a score from 0 to 3 to be added to the written vote).
Teaching tools
Company case studies. Visit of the students in a company for the execution of the group project carried out on a real business case.
Office hours
See the website of Cristina Mora
SDGs
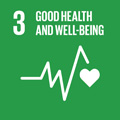
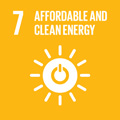
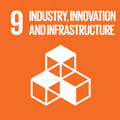
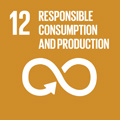
This teaching activity contributes to the achievement of the Sustainable Development Goals of the UN 2030 Agenda.