- Docente: Angelo Casagrande
- Credits: 13
- SSD: ING-IND/21
- Language: Italian
- Moduli: Angelo Casagrande (Modulo 1) Carla Martini (Modulo 2)
- Teaching Mode: Traditional lectures (Modulo 1) Traditional lectures (Modulo 2)
- Campus: Ravenna
- Corso: First cycle degree programme (L) in Chemistry and Technologies for the Environment and Materials (cod. 8515)
Learning outcomes
Metal Science
The aim of the course is to give the students a sound knowledge of the different classes of materials in order to:
a) understand the relationship between structure, microstructure and materials properties,
b) identify the technologies more suited for a material to be transformed into a industrial product,
c) be acquainted with the available techniques for analysis and testing of materials.
Materials technology
This course provides the basic knowledge about the technology of manufaturing processes of metallic and ceramic components
Laboratory
Upon successful completion of the course, the student gains skills for planning an experimental campaign aiming at the characterisation of structure and properties of materials. In particular, students will be able to: (a) select which techniques should be used for the microstructural and mechanical characterisation of different classes of materials, keeping into account international standards and (b) evaluate and discuss the results on the basis of correlations between structure-microstructure and properties.Course contents
Metal Science
Materials science as a link between theoretical and applied disciplines. Materials classification and evolution. Competition and sinergy between materials. Resources and reserves of materials. Energy content and environmental impact of materials. Disposal and recycling of materials.
Materials structure and microstructure. Structure and interatomic bond: covalent, ionic and metallic solids. Intra- and intermolecular bonds in polymeric solids. Crystal structure of metals: CFC, HCP and BCC lattices. Crystal structure of ionic ceramics. Diamond and covalent solids. Silica and silicates. Crystallinity in polimeric solids. Non-crystalline solids: inorganic glasses and amorphous polymers. Crystal systems and unit cells. Indices of positions, directions and planes in the cubic cell. Structural analysis by XR diffraction techniques. Structure defects in crystalline solids: vacancies, interstitials, dislocations and grain boundaries.
Structure-related properties: density, thermal expansion and elastic behaviour. Elastic moduli and interatomic bond strength. The stiffness of macromolecular solids: thermoplastics, thermosettings and fibers. Elastomers. Elastic properties of composite and foamed materials. Anelasticity and viscoelasticity.
Materials microstructure: components, phases and micro-constituents. Substitutional and interstitials solid solutions. Intermediate phases and compounds. Free energy vs. composition diagrams. Binary equilibrium diagrams of metals and ceramics. Ternary diagrams in ceramic technology. Copolymers and polymer blends. Nanostructured materials and related technologies.
Solidification of metals: homogeneous and heterogeneous nucleation. Growth morphology and solidification microstructures. Metal forming by casting techniques. Microstructure and defects of metal castings. Crystalline solidification and glass transition. Vitrification of silicate melts. Liquid-phase sintering. Microstructure of polymeric materials. Injection moulding and reactive solidification of polymer melts. Film formation in paints and adhesives. Slip casting. Setting and hardening of lime, plaster and cement mortars.
Diffusion controlled solid-phase transformations. The austenite to pearlite transformation. Precipitation from solid solutions. Sintering and devitrification.
Theoretical strength of materials. Plastic deformation of metals: dislocations and slip systems. Yield strength, strain hardening and tensile strength of metals. Strengthening mechanisms in metal alloys. Cold forming of metal components. Recrystallization and grain-growth Hardening and heat treatments of alloy steels. Precipitation hardening of aluminum alloys. Plastic deformation and cold drawing of polymeric materials. Plastic forming of ceramic pastes.
Rupture strength of ceramic materials: the Weibull modulus. Ductile and brittle fracture. Impact and fracture thoughness. The fatigue rupture and creep of materials. Hot forming of metals. Glass forming. Extrusion and thermoforming of plastomers. Moulding of thermosetting polymers.
Physical properties of materials. Electronic energy bands in solids: conductors, semiconductors and insulating materials. Superconductors. Conductive polymers. Intrinsic and extrinsic semiconductors. Semiconductor-based devices. Dielectric properties: insulators and condensators. Piezoelectricity and electrostriction. Magnetic properties. Soft and hard magnetic materials. Electromagnetic transducers. Optical properties: photonic materials and systems. Thermal properties: capacity, conductivity and expansion coefficient. Thermal shock in ceramics.
Degradation, corrosion and aging of materials. Wet and dry corrosion of metals. Active and passive protection techniques. Thermal and photochemical degradation of polymeric materials. Chemical corrosion of ceramic materials.
Materials technology
- Metals
Fundamentals of Metalworking: forging, rolling, extrusion, drawing tubes, sheet metal forming.
Casting Processes: sand casting, permanent mold casting, continuous casting
Metal joining techniques: Oxyacetylene welding, Gas-tungsten arc welding, Gas-metal arc welding, laser beam welding, resistance welding. Metals machining.
- Ceramic Materials
Preliminar size reduction of solids: Rotary dryers, coarse crusher, crushing rolls, solid mixing machines .
Dry grinding: hammer mill, Raymond mill, ball mill .
Wet grinding: Alsing mill, continuous mill .
Screening: rotary screen, vibrating screen, vibro-energy screen, air classifiers, hydrocyclone.
Continuous mill cycle, filter press, spray dryers, granulators, press-system, extruders .
Drying: Tray dryer, tunnel dryer, horizontal roller dryer, vertical in-line dryer .
Firing: Tunnel kiln, shuttle kiln, kiln single and double layers .
Handling: TGV, supervisor system .
Air cleaning: Cyclone separator, bag filter, electrostatic precipitator, Venturi washer .
Conveying of bulk solids: roller conveyor, belt conveyor, bucket elevator, screw conveyor, pneumatic conveyor
Laboratory
- Generalities on the structure of crystalline materials: X-Ray diffraction.
- Practical introduction to phases and phase diagrams: the generation of microstructures.
- Sampling procedures and preparation of samples for microstructural analysis.
- The Fe-C phase diagram and the equilibrium microstructures of ferrous alloys. Metallographic preparation of steel and cast iron samples followed by optical microscope observation. Image Analysis techniques and generalities on quantitative metallography.
- High magnification microscopy techniques: SEM, TEM, AFM. SEM observation of metallic and ceramic materials coupled with localised EDS microanalysis.
- Thermal analysis: DSC, TGA, dilatometry.
- Mechanical properties of materials: tensile tests on polymeric and metallic materials; flexure strength and fracture toughness measurements on ceramic materials; micro-hardness tests on metallic and ceramic materials.
Readings/Bibliography
Slides of the course (available in https://iol.unibo.it for the laboratory module).
William F. Smith : “SCIENZA E TECNOLOGIA DEI MATERIALI” Ed. McGraw Hill, 2004
W.D:Callister: “SCIENZA E INGEGNERIA DEI MATERIALI” EdiSES-Napoli 2003
W.Kurz, J.P.Mercier, G.Zambelli “INTRODUZIONE ALLA SCIENZA DEI MATERIALI” Hoepli Ed. 1997
M.F.Ashby, D.R.H:Jones “ENGINEERING MATERIALS” 2 Voll Butterworth-Heinemann Ed. 1997
D.Askeland “ THE SCIENCE AND ENGINEERING OF MATERIALS” 3°Ed. Pergamon 1996
AA.vari “MANUALE DEI MATERIALI PER L'INGEGNERIA” Ed. McGraw Hill
M. Santocchi, F. Giusti "Tecnologia Meccanica e studi di fabbricazione", 2000, Casa Editrice Ambrosiana.
W.D. Callister, D.G. Rethwish "Materiali per l'ingegneria civile ed industriale", Edises (2015).
D.R. Askeland, P.P. Fulay, W.J. Wright "Scienza e tecnologia dei materiali", Città studi (2017).
Dieter, G.E., Mechanical metallurgy, 1988, SI metric edition, McGraw-Hill
Edwards, L. and Endean, M., Manufacturing with materials, 1990, Butterworth
Heinemann Lange, K., Handbook of metal forming, 1985, R.R Donnelly & Sons Company,
Beddroes, J. Bibbly M.J., Principles of metal manufacturing processes, Arnold
G.P. Emiliani, F. Corbara, Tecnologia Ceramica, 1999, Faenza Editrice
Preparazione materie prime e formatura di p.c., 2008, S.A.L.A. Editore Modena
Essiccazione e cottura di piastrelle ceramiche, 2008, S.A.L.A. Editore, Modena
V. Petrone, E. Fiocco. L'impianto Chimico, 2000, Siderea, Roma.
Teaching methods
Lectures and practicals according to the timetable.
Assessment methods
The final examination of the course, which aims to achieve the objectives, consists of the synthesis of final evaluations of the different modules:
Laboratory of Metal Science, Materials Technology and Metal Science.
The section of Materials Technology consists of a written test, 30/30, for testing knowledge of techniques of production of metallic and ceramic artifacts.
The section regarding the Laboratory, consists of the elaboration of written lab reports, 30/30, and assesses the ability to choose appropriate techniques for the determination mechanical properties and microstructures of materials;
The Metal Science section, consists of an oral exam, 30/30, with a general comparison of mechanical, chemical and physical properties of metallic, ceramic and polymeric materials.
The final score of the course, obtained by the candidate, will be formed by the weighted average obtained from assessments of each section, which shall not be less 18/30. In the event that the candidate does not reach the minimum target of knowledge in a section of course, this will have to be repeated and overcome, so as to achieve the total final evaluation
Teaching tools
PC and projector, blackboard, notes and sets of university lectures.
Teaching lab (equipment for materialographic preparation; optical and stereo microscopy with image analyser; micro-hardness tester; tensile tester) and research labs (XRD, SEM/EDS, 4-point bending tester).
Office hours
See the website of Angelo Casagrande
See the website of Carla Martini
SDGs
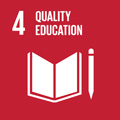
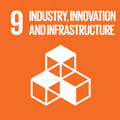
This teaching activity contributes to the achievement of the Sustainable Development Goals of the UN 2030 Agenda.