- Docente: Marco Troncossi
- Credits: 6
- SSD: ING-IND/13
- Language: English
- Moduli: Vincenzo Parenti Castelli (Modulo 1) Marco Troncossi (Modulo 2)
- Teaching Mode: Traditional lectures (Modulo 1) Traditional lectures (Modulo 2)
- Campus: Bologna
- Corso: Second cycle degree programme (LM) in Advanced Automotive Engineering (cod. 9239)
Learning outcomes
Students learn the basic elements for modelling the kinematics, the statics and the dynamics of spatial articulated systems with both open (serial) and closed (parallel) architectures, which the current industrial robots is based on.
In addition, the students learn basic knowledge of criteria of use, motion planning, as well as economic and organizational aspects that are needed to integrate robots into production systems.
Course contents
The course is organized in the following main sections:
- ORIGINS AND HISTORY OF ROBOTS (1 hour). Introduction. Origins. State of the art of Robotics. Classification of robots. Aim of industrial Robotics. Main issues of industrial robotics. Precision and calibration.
- STRUCTURE AND GENERAL CHARACTERISTIC OF ROBOTS (4 hrs). Introduction. Structure of a robot. The manipulator. End effectors. Actuators. Sensors. Controller. Programming methods and languages. Main characteristics of an industrial robot.
- COORDINATE TRANSFORMATION MATRICES (8 hrs). Introduction. Position and orientation of a rigid body and reference systems. Matrices for the transformation of the coordinates. Rotations and translations. Homogeneous transformations.
- KINEMATICS OF MANIPULATORS (15 hrs). Introduction. Kinematic model of a manipulator. Matrices of Denavit-Hartenberg. Kinematic equations. Direct and inverse kinematic problem. Jacobian of a manipulator. Singularities.
- STATICS OF MANIPULATORS (1 hr). Introduction. Analysis of forces and motion. Force and moments balancing.
- DYNAMICS OF MANIPULATORS (13 hrs). Introduction. Recall of rigid body dynamics. Equation of motion. Direct and inverse dynamic problem.
- PARALLEL MANIPULATORS (4 hrs). Direct and inverse kinematic analysis. Singularities. Kinetostatic and dynamic analyses.
- TRAJECTORY PLANNING (2 hrs). Introduction. Generalities on the generation and description of the trajectory. Trajectory generation in joint and Cartesian space. Trajectory planning based on the dynamic model.
- MANIPULATOR CONTROL (4 hrs). Introduction. Position control; Velocity control; Force control. Control systems of existing industrial robots.
- MANAGEMENT AND ECONOMIC ASPECTS (hints) (2 hrs). Industrial robotics standards. Organization and automation impacts on production and workers' qualification.
Problems and applications (6 hrs.):
- Inverse position analysis of PUMA
- Position analysis of "6-6" parallel manipulator.
- Elements of Dynamics
- Dynamic analysis of a 2R spatial manipulator
- Trajectory planning
Readings/Bibliography
Reference book
- Siciliano B., Sciavicco L., Villani L., Oriolo G., Robotics: Modelling, Planning and Control, Springer, 2009.
Suggested book
- Siciliano & Khatib eds., Handbook of Robotics, Springer, New York, 2008
In-depth readings
- Tsai L.W., Robot Analysis, The Mechanics of Serial and Parallel Manipulators, John Wiley & Sons, 1999.
- Merlet J.P., Parallel robots. Kluwer, Dordrecht, 2000.
- Nof S.Y., Handbook of Industrial Robotics, 2nd ed., John Wiley & Sons, 1999.
- Engelberger J.F., Robotics in Practice: Management and applications of industrial robots, Avebury Publishing Company, 1980.
- Craig J., Introduction to Robotics, Mechanics and Control, 1989, Addison-Wesley Publishing Company.
- Erdman and Sandor, Analysis and Synthesis of Mechanisms, voll. 1 and 2, 1990, Prentice-Hall.
- Suh C.H. and Radcliffe C. W., Kinematics and Mechanisms Design, John Wiley & Sons, 1978.
- Sandler Ben-Zion, Robotics: Designing the Mechanisms for Automated Machinery, Academic Press, 1999.
- Rivin, E. I. Mechanical design of Robots, McGraw-Hill, 1988.
Teaching methods
The course includes:
- Theoretical lectures conducted on the blackboard and with the aid of multimedia systems.
- A complete cycle of exercises and illustration of industrial applications that combines and integrates theoretical lessons.
Connection in videostreaming (TEAMS) is available for students attending the lessons remotely. The videos of the lessons are recorded and subsequently made available on the Panopto platform, whose link will be made available on the course webpage on https://virtuale.unibo.it (see Teaching tools).
Assessment methods
The assessment of student learning is carried out at the end of the course by a written test on the main topics of the course.
The written exam is based on a number of questions (typically three to five), including both exercises and theory questions.
The final score is computed as the arithmetic mean of the single scores obtained for each question. The positive evaluation of at least two single questions is mandatory to consider the examination successfully passed.
Teaching tools
Slides are used as a support for the lesson presetations. Pdf files of the presentation (along with suggested readings, lesson notes and additional supplementary material) are available at https://virtuale.unibo.it
Lessons taught in lecture room and in informatic lab. Connection in videostreaming is available for students attending the lessons remotely.
In consideration of the type of activity and the teaching methods adopted, the attendance of this training activity requires the prior participation of all students in the training modules 1 and 2 on safety, in e-learning mode.
Links to further information
https://www.unibo.it/sitoweb/marco.troncossi
Office hours
See the website of Marco Troncossi
See the website of Vincenzo Parenti Castelli
SDGs
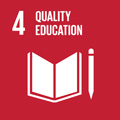
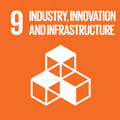
This teaching activity contributes to the achievement of the Sustainable Development Goals of the UN 2030 Agenda.